This article briefly reviews the development history of cone crusher, discusses the structure and performance of hydraulic cone crusher.
Through the analysis and application example investigation, it is not difficult to find that the hydraulic cone crusher is not only reliable, but also efficient. It is an ideal medium fine crushing equipment of the new generation of crushing and screening technology.
1. Development History Of Cone Crusher
In the late 1920s, with the continuous progress of the industrial revolution, in order to meet the needs of industry for raw materials, the continuous expansion of the scale of mining industry and the continuous maturity of beneficiation technology, cone crusher as medium and fine crushing equipment appeared.
The first generation of cone crusher is the spring cone crusher, which was invented by Symons brothers of the United States and developed and produced into a series of Symons series products by Nordberg company. It has been widely used all over the world. At present, it is also used in old mines and users who do not have high requirements for equipment performance.
The first generation cone crusher adopts eccentric sleeve to drive the moving cone, with large eccentricity, low swing frequency, small driving power and spring overload protection. The main problems are:
- The iron overload protection stroke of the spring is small;
- The rotation speed of the main shaft and moving cone assembly must be limited to avoid burning the copper sleeve;
- Once the crushing cavity is blocked, it is difficult to clear the cavity;
- It is not convenient to adjust the ore discharge port;
- Fixed cone disassembly takes a long time;
- Water ring sealing water is often mixed with lubricating oil, resulting in waste of lubricating oil.
In order to overcome the problems of difficult adjustment of ore discharge opening, difficult cavity cleaning and poor overload protection of spring cone crusher, as early as the late 1940s and early 1950s, allis-Chalmers company of the United States launched hydrocone single cylinder hydraulic cone crusher;
In the late 1950s and early 1960s, Kobe and other companies in Japan added a hydraulic system on the basis of the spring cone crusher to help adjust the ore discharge opening and cavity cleaning.
In the late 1970s and early 1980s, with the continuous improvement of steel-making technology and material properties, Nordberg company of the United States introduced omnicone cone crusher by replacing mechanical spring with hydraulic spring. Compared with mechanical spring cone crusher, omnicone cone crusher has the following advantages:
- Hydraulic cylinder replaces spring, iron passing stroke is increased and reliability is improved;
- The main shaft is separated from the moving cone, and the main shaft is changed to fixed type, short and thick cylinder, with large bearing capacity; The crushing speed (swing frequency of moving cone) is improved;
- Two way acting hydraulic cylinder to clean the crushing chamber in a few minutes;
- The hydraulic push rod regulates the ore discharge port, and the hydraulic push rod assists in removing the cone assembly;
- Cancel the water ring seal and replace it with patented non-contact Tu seal;
- Increased input power;
- The standard type and short head type of medium and fine crushing equipment have one moving cone, which can match 6 ~ 8 kinds of lining plate cavity shapes.
Although many companies launched new cone crusher products in the 30-40 years before the late 1980s, they did not really shake the dominant position of spring cone crusher.
Since the late 1980s, with the wide application of computer technology, HP series and MP series of multi cylinder hydraulic cone crushers represented by Metso Nordberg company and H and GP series of single cylinder hydraulic cone crushers represented by Svedala and Metso Nordberg company in Sweden have basically replaced spring cone crushers in the equipment selection of new projects. The wide application of hydraulic cone crusher marks the arrival of the second generation cone crusher.
2. Mechanical Structure Of Hydraulic Cone Crusher
Hydraulic cone crusher can be divided into spindle fixed type and spindle floating type according to different adjustment modes of ore discharge port. The adjustment of the discharge opening of the spindle fixed hydraulic cone crusher is to adjust the discharge opening by moving up and down through the rotation of the fixed cone screw.
The advantage of this adjustment method is that the discharge opening is easy to lock, and its representative series are HP and mp; The discharge port of the spindle floating hydraulic cone crusher is adjusted by floating the spindle up and down. The disadvantage of this adjustment method is that it is difficult to lock the discharge port when crushing hard ore. its representative series are h and GP.
Main shaft fixed multi cylinder hydraulic cone crusher
Metso Mining Machine inherits and develops on the basis of spring cone crusher (i.e. SYMONS). Through the production practice of omnicone multi cylinder hydraulic cone crusher, it has developed spindle fixed hydraulic HP and MP cone crushers with exclusive intellectual property rights.
Compared with the single cylinder hydraulic cone crusher, the spindle fixed hydraulic HP and MP cone crushers have large crushing force, high crushing frequency, slow slope, high finished product rate and fine ore content. See the following picture for their mechanical mechanism.
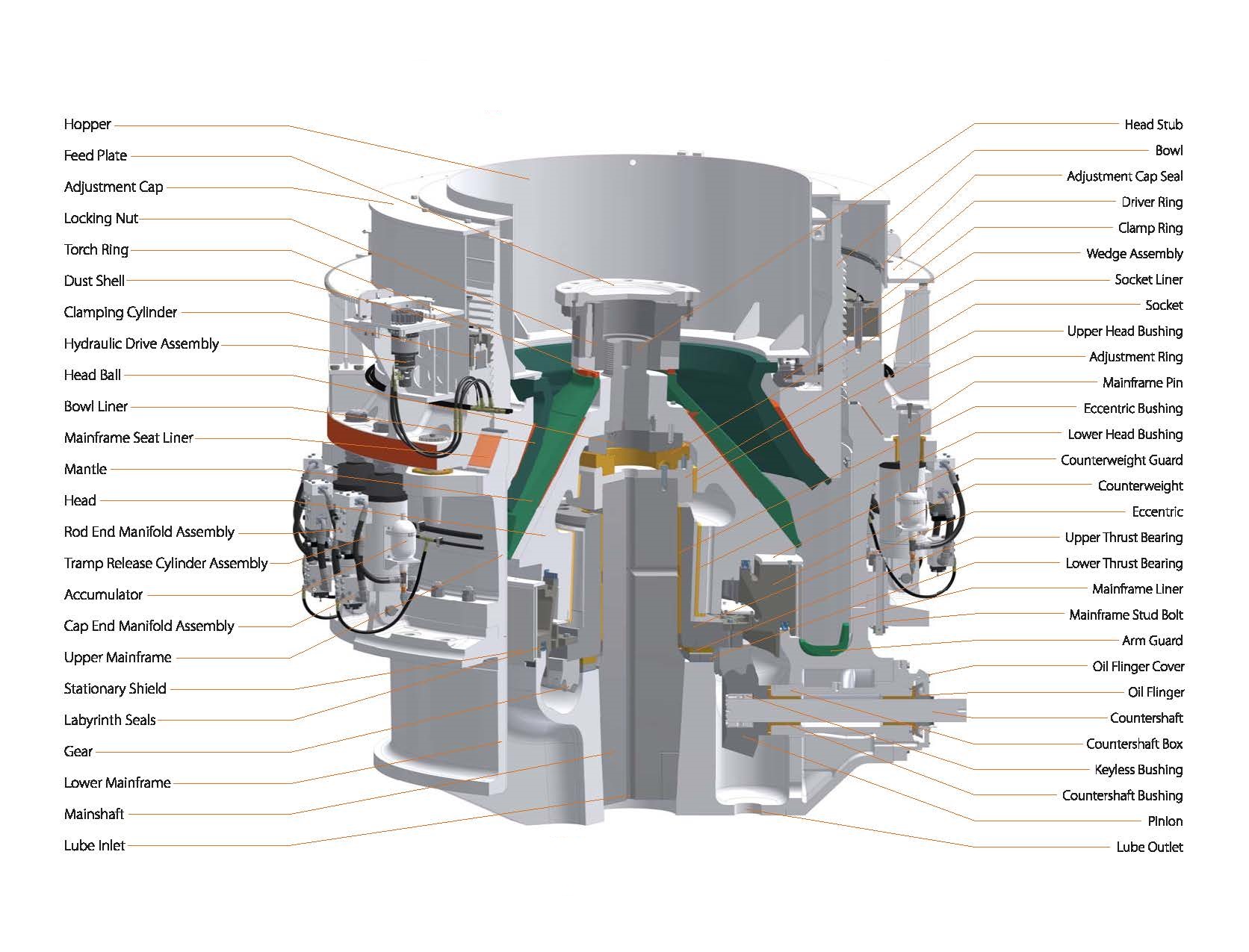
The main shaft of the multi cylinder hydraulic cone crusher is fixed on the base of the lower frame, the eccentric assembly is complete on the main shaft, and rotates around the main shaft driven by the pinion transmission assembly.
The moving cone assembly is placed on the top of the thousand spindle through the ball bearing and swings under the drive of the eccentric assembly. The adjusting ring is placed on the lower frame and connected with the base of the lower frame through the peripheral hydraulic cylinder.
After the adjusting action of the adjusting cone or the adjusting cone of the hydraulic cylinder is completed, and the locking plate is replaced.
Further optimization of HP Hydraulic Cone Crusher Based on omnicone hydraulic cone crusher:
- Increase the eccentricity and improve the position management ability;
- Speed up the crushing frequency, increase the power and improve the crushing fineness;
- Raise the center of the rotating cone pendulum to optimize the cavity design;
- The lining plate is thickened to prolong the service life;
- The hydraulic motor replaces the hydraulic push rod device, and the ore discharge port is adjusted accurately and continuously;
- Driven by hydraulic motor, remove the fixed cone assembly within 10 minutes;
- Key components are made of high-strength materials, with appropriate weight increase and better reliability.
When the multi cylinder hydraulic cone crusher is crushing, the crushing force is transmitted to the lower frame base through the main shaft, adjusting ring and surrounding hydraulic cylinders. The main shaft bears the pressure winding stress, and the whole main frame is not subject to tensile stress.
Under the pull of the surrounding hydraulic cylinder, the main frame also bears the compressive stress, and its value is the downward pull force of the surrounding hydraulic cylinder minus the crushing load, so the stress on the side wall of the lower frame becomes smaller during crushing.
Main Shaft Floating Single Cylinder Hydraulic Cone Crusher
The structure of the single cylinder hydraulic cone crusher is similar to that of the rotary crusher. The beam, fixed cone assembly and frame are fixed, and the main shaft and moving cone float up and down together to crush the ore driven by the deflection assembly. The mechanical structure of the spindle floating single cylinder hydraulic cone crusher is shown in the following picture:
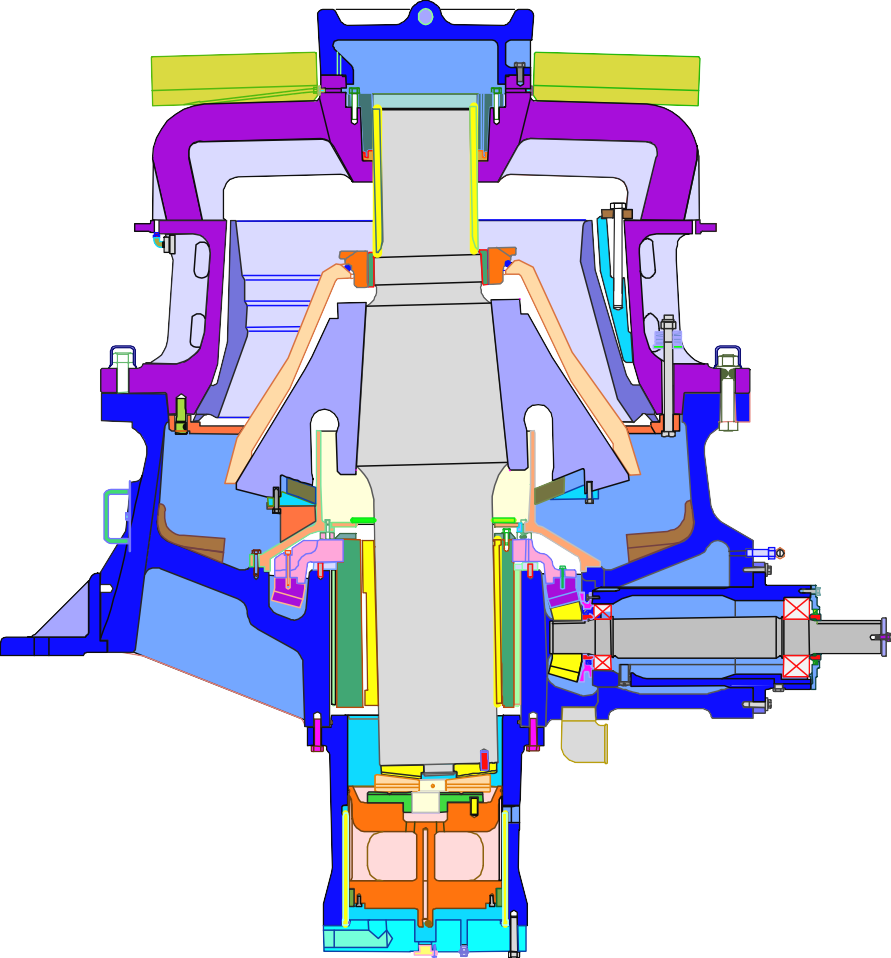
When the single cylinder hydraulic cone crusher is crushing, the crushing force exerted by the bottom hydraulic cylinder is transmitted to the beam, upper frame, middle frame and lower frame through the main shaft and fixed cone assembly. The main shaft bears compressive stress, the cross beam bears winding stress, and the whole main frame bears tensile stress.
Hydraulic Cone Crusher Structure And Mechanical Strength
Single cylinder hydraulic cone crusher and multi cylinder hydraulic cone crusher have different mechanical structures, and the stress on the frame is very different when crushing ore. The frame of single cylinder hydraulic cone crusher bears tensile stress, while the frame of multi cylinder hydraulic cone crusher bears weakened compressive stress.
According to the relevant knowledge of engineering mechanics, the allowable compressive stress of plastic rigid materials is usually 1.5 ~ 2.5 times of the allowable tensile stress, that is, the pressure borne by the same cut steel can be 1.5 ~ 2.5 times greater than the tensile force.
It makes sense that the single cylinder hydraulic cone crusher was bulky in the early frame. At present, there are still companies in the world, such as Krupp company, which still practice this practice, while Sandvik’s H-series single cylinder hydraulic cone crusher and Metso’s GP series single cylinder hydraulic cone crusher develop light single cylinder hydraulic cone crusher.
Metso’s GP series single cylinder hydraulic cone crusher in Finland adopts vacuum smelting technology in frame casting to improve the tensile strength of the frame in order to overcome the insufficient tensile strength of the frame caused by lightness, while Sandvik’s H series single cylinder hydraulic cone crusher still uses ordinary smelting technology.
Therefore, the frame cracking of Sandvik’s H-series single cylinder hydraulic cone crusher has occurred from time to time in the Chinese market recently. For example, the organic frame and beam cracking have occurred in Dexing Dashan Concentrator, Meishan Iron Mine, Anshan mining company, apple aluminum, Lala copper mine, luolvtuotuan, Hunchun gold mine and other mines.
The cracking of the frame of a typical single cylinder hydraulic cone crusher is shown in the following picture.
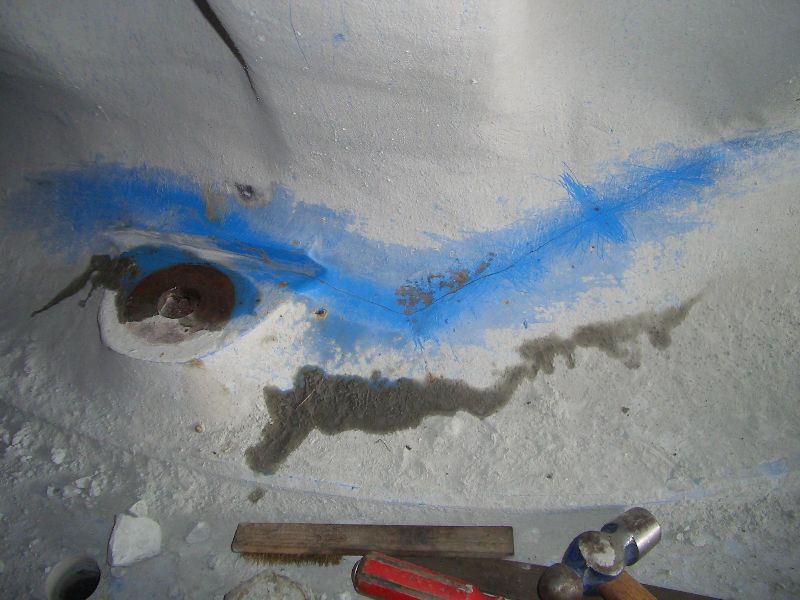
The spring cone crusher is stressed by a thousand frame, so the frame must be heavy and solid.
The HP series multi cylinder hydraulic cone crusher developed on the basis of spring cone crusher is free from tensile stress by 1000 frames, so it can be developed in the direction of lightweight. Although the HP series cone crusher can be made lighter, the stress is at the connection between the surrounding hydraulic cylinder and the lower frame base, and it is pulsating when the load is overweight, so the HP700 frame launched in the early stage has problems there.
On the basis of production practice, Metso mining machine has completely updated the design, strengthened and thickened the key parts of HP series multi cylinder hydraulic cone crusher. For thousands of extra large mines, meizhuo mining machine also launched MP series multi cylinder hydraulic cone crusher to simplify the crushing and screening process.
The progress of modern material technology has also created conditions for the lightweight of hydraulic cone crusher, such as vacuum metallurgy technology. Although the technology of metallurgical materials has been improved, the lightness of hydraulic cone crusher must consider the crusher structure.
The lightness degree of hydraulic cone crusher with different structures cannot be the same. It must be reasonable and lightness in order to ensure the safety and reliability of the equipment.
Mechanical Structure And Parameters of Hydraulic Cone Rrusher
Hydraulic cone crushers with different mechanical structures adopt different combinations of crushing parameters in order to achieve the best crushing effect. The spindle fixed multi cylinder hydraulic HP and MP cone crushers have a gentle gradient and a long parallel belt, so they must operate with large deviation, high frequency and large ore discharge outlet;
The spindle floating single cylinder hydraulic cone crusher has steep gradient and short parallel belt, so it must operate with small eccentricity and small ore discharge port. Only in this way can the processing capacity and discharge fineness of the crusher achieve the best comprehensive effect.
The main shaft floating single cylinder hydraulic cone crusher is limited by its own structure and can not effectively operate at a small ore discharge port. The operation of small ore discharge opening often means large crushing force.
The 1000 spindle floating single cylinder hydraulic cone crusher adopts the structure of rotary crusher, but the heavy design of rotary crusher is not adopted, so the spindle floating single cylinder hydraulic cone crusher can not provide large crushing force. Therefore, in the actual production and operation, the spindle floating single cylinder hydraulic cone crusher shows that the discharge opening can not be locked. In case of hard ore, the rack is often cracked in order to lock the discharge port.
The discharge port of the main shaft floating single cylinder hydraulic cone crusher is not locked. Even if sufficient motor power is installed, the electric power cannot be effectively input into the crusher for crushing operation. Therefore, the output of qualified crushing products is low and the content of fine ore is small.
Although the basic working principle of cone crusher is the same, the structures of various cone crushers are different, so the crushing performance in actual production is still different, because the structure determines the performance.