Function principle of HPGR Mill
High Pressure Grinding Roller Mill, i.e. HPGR mill, the working principle of HPGR mill is using two horizontal arranged roller turning in opposite direction and press crushing material layer, refer to sketch 1-1, the material layer in enclosed environment is forced moving down, during this process, pressure is continuously increasing, until it is crushed and pressed to solid bricks, coming out from bottom side.
The mechanical intensity is quite small, it can be broken by bare hands. Material bricks content many fine powders, fine material which is less than 90m occupied 20~30% percentage. Inside structure of rough material is already destroyed, the crushed material has many cracks, grindability is high, in other word, in pressing crushed material bricks, size less than 2mm material occupy 60~70%,and those material with many minor cracks.
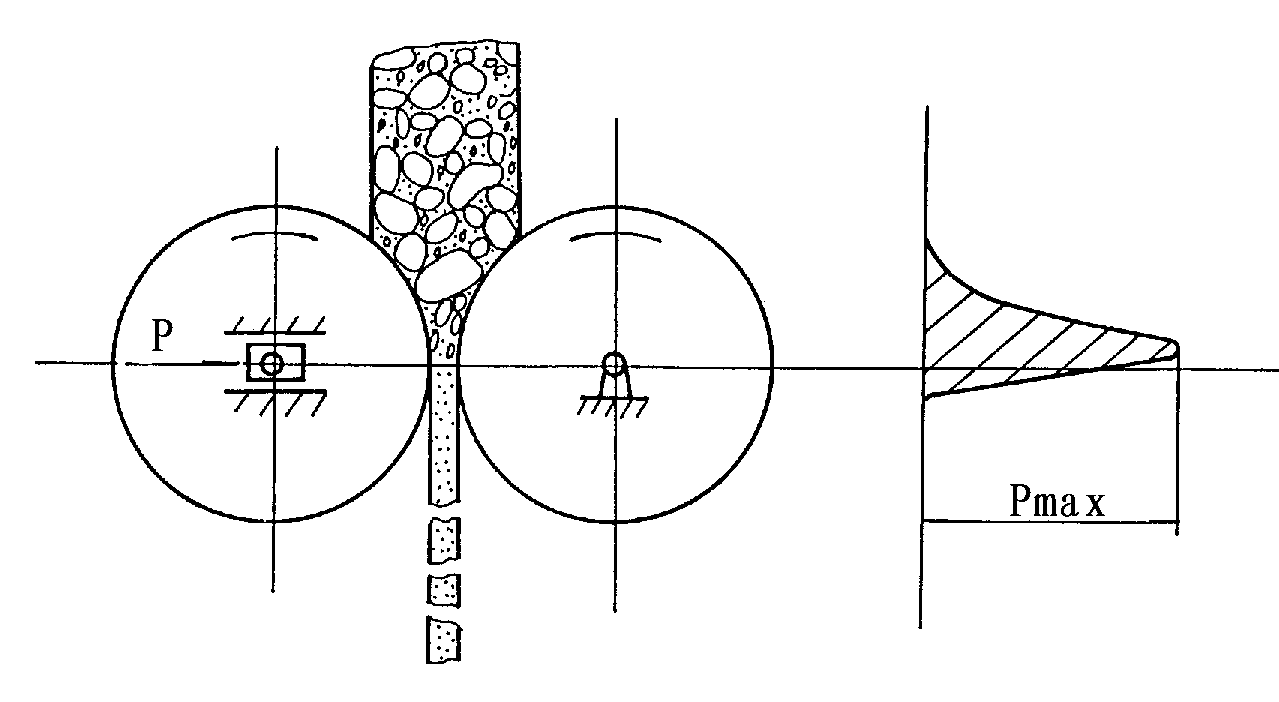
Sketch 1-1 Function principle of HPGR Mill
The appearance of HPGR mill is similar to roller crusher, both of them have two rollers which is turning in opposite direction, pushed by force coming from outside, the material is “crushed”, but their working principle is totally different.
The principle of HPGR mill is, high pressure, material layer and crushing. Compare to crusher:
- The hydraulic system of HPGR mill may provide very high pressure, up to hundred thousand tons, i.e. high pressure.
- The crushing type is not single grain crushing, the material is limited in enclosed space and press to each other and thus forming high pressure material layer for crushing, this is also the reason why HPGR mill has advantage in energy saving.
Main Parts of HPGR Mill
HPGR mill is consisted by motor, planetary gearbox, roller, support of roller, machine frame, torque support, pressure increasing device of hydraulic system, lubrication system, material feeding unit.
Two roller were derived by two separate motor through planetary gearbox. Rollers and planetary gearbox are connected by expansion sleeve. One roller is active roller and the other is fixed roller, roller shaft is made of high strength forged steel, roller surface is mounted with roller nails.
Machine frame assembly
Machine frame is the base for fixing the other parts of HPGR mill , mainly consisted by upper frame, lower frame, middle body and end parts, all of them is welded steel structure, and connected by bolts and shear pins.
Considering level floating requirements of active roller, guide sliding key is designed on lower frame, in contacting surfaces, measurements should be taken to decrease friction, such us, arrange lubrication oil channel, apply polyfluortetraethylene plate etc. The connection of machine frame is high strength bolting connection, when tightening should be strictly in accordance with the requirements of the tightening torque.
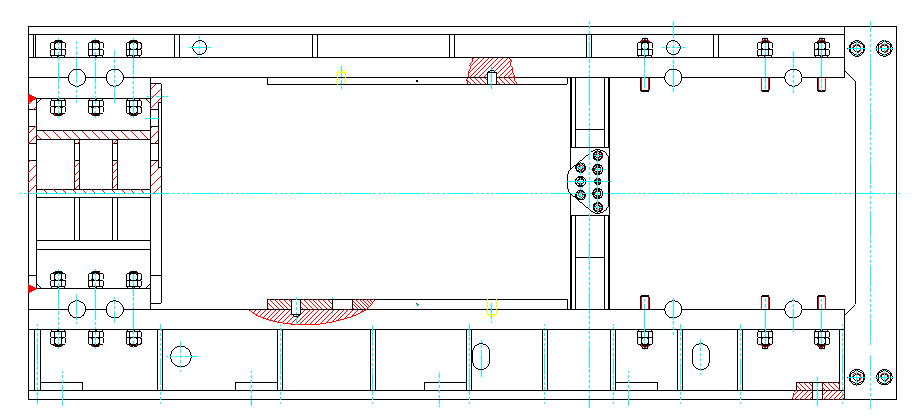
Sketch 1-2 Machine frame assembly
The end parts are used for fixing the hydraulic loading device, and a hydraulic pipeline through hole is provided in those end parts. On middle parts there is support pole for supporting the lower material buffer plates, the length of support pole can be adjusted through connecting screw thread, and release impacting force through disc spring.
Pressing Roller Assembly
Pressing roller assembly is consisted by roller shaft, roller sleeve, bearing, bearing house and sealing rings etc.
Two opposite rotation of the squeeze roller is the core component of the HPGR Mill, and they are also the key factor which decide the performance of HPGR Mill. Squeeze roller is the most difficult manufacturing part, and required longest fabrication time, the squeeze roller is mainly consisted by roller sleeve and welded anti-wearing layer.
The roller sleeve and the roll shaft must be made of best quality alloy steel material, and must be applied by complex heat treatment and strict flaw detection, to ensure that the quality reach the requirements. Because the acted force is extremely great, roller surface must be applied with high hardness anti-wearing nails.
On both ends of each pressing roller are supported by rolling bearing device. Due to work load on the main bearing is large and frequent fluctuations in the material layer, generally, we use four cylindrical roller bearings, and reinforced kind, the requirements of bearing sealing and lubrication cooling is pretty high. Such kindly of bearing has smaller diameter, bigger width, high carrying capacity, but without self-alignment .
The gap between two rollers can be adjusted based on different material, in addition, crushed material always unavoidably mixed with some hard articles such as iron material etc, so the roller gap must be designed into adjustable kind. From the structure side, one roller is fixed, i.e. fixed roller, while the other roller is movable in horizontal direction , forward or backward, or moving in incline status, which is called active roller. The moving of active roller is realized through special bearing house in machine frame.
Inside of press roller bearing house, we designed cooling water circulation channel, which will provide reliable condition for temperature control of bearing. Because the bearing house should frequently moving on machine frame, so the upper and lower surface should applied with polyfluortetraethylene plate to decrease friction factor.
Heat resistance which installed on the end of bearing house is for measurement of temperature of main bearing, it is close touching outside ring of bearing, worked together with electrical control system, the continuously temperature detection can be ensured, the alarm temperature is also set to control the bearing temperature.
Squeeze rollers is the most important part of HPGR mill, the working surface of roller is easily in wearing, so regular check and timing repairing must be applied.
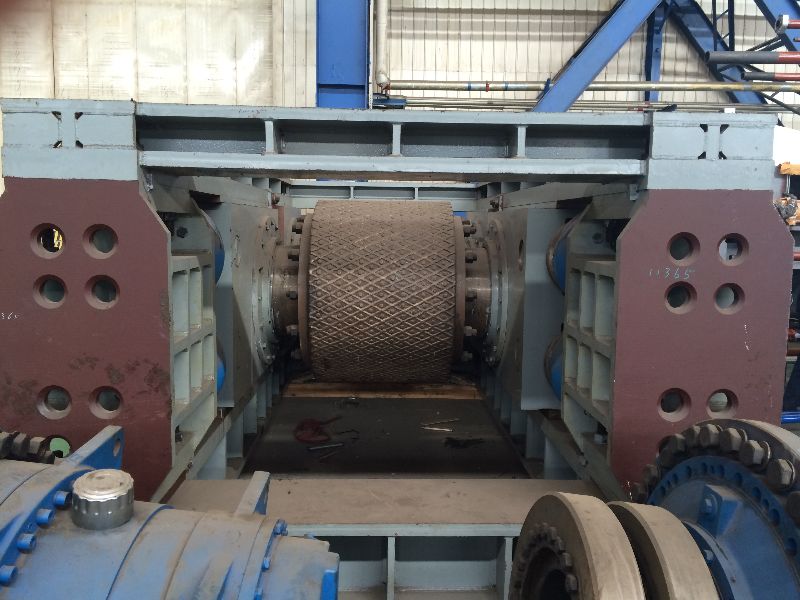
Squeeze Rollers
Material Feeding Device
HPGR mill is the equipment to realize high pressure grinding material layer , which must be equipped with following condition:
Hopper
- Volume of feeding material must be bigger than discharging material, in the other word, above the minimum gap of two rollers, material must be fully filled in width direction, and guarantee continuously material feeding, if lost continuously material feeding or material grain between other has untouchable space, then the HPGR mill have no difference between traditional double roller crusher.
- Thus, in material feeding direction, certain height material column must be maintained , use the gravity of material column to fill the gap between the rollers, or arranging a vertical reamer above press rollers to force material feeding, which will create bigger material feeding force, increase producing capacity and decrease the relative movement between roller and material, thus decrease wearing of roller surface.
- To adjust material feeding capacity of HPGR mill and match whole grinding system, material feeding hopper equipped with adjustable valve plates to change material feeding, such valve plate is a very important method, which is capable to adjust material feeding capacity and required power in certain scope, i.e. crushing grinding power, without affect operation pressure of roller, keep stable operation of HPGR mill.
- Because of different grinding material , the roller gap also need to be changed, and passing through capacity is also different. However, there could be only one size of discharge hopper , so the flexibility of HPGR mill is limited. With adjustable feeding valve plate, the adaptability of mill increased a lot, as the roller gap can also be adjusted, which will make the rollers working in settled pressure in normal operation.
- Such structure in adjusting of feeding valve plate is not complicated, use hand wheel and adjusting screw pole, the valve plates can move up and down, and thus change the width material feeding hopper.
- Normally, material feeding hopper is designed into narrow steel plate welded structure, above the two rollers in proper height to reach the requirement for forming material column, at the same time, not creating material block phenomenon. Fragile material is more easier to reach such requirements, but for the material contains more water and ash, the squeeze result will be affected and more easier in creating material block, under such circumstance, such material should be removed in advance to ensure good performance of HPGR mill.
Side Buffer Plate
Squeezing material of HPGR mill is kind of high pressure operation, material is easier coming out from gap and ends of two rollers. Such squeezed out material, due to less pressing, most of them material size is bigger.
In practical operation, in squeezed material, which material size is bigger than 2mm is caused by roller end leaking. This will badly affect the grinding efficiency and bring great operation difficulty, especially to narrow roller HPGR mil, sometimes, this part of material will be sent back for re-grinding, although such action solved the problem of too much bigger material size, but greatly affected the grinding efficiency.
Therefore, add side buffer plate at ends of roller have very good performance, to ensure proper pre-pressure of buffer plate, there is disc-spring in adjusting position, this will decrease impacting and vibration caused by inhomogeneous material .
Drive Unit and Torque Support
Drive unit is consisted by gearbox, fluid coupling, flexible coupling, expansion coupling, motor and lubrication system, due to extreme high pressure, two press roller used separate driving system, i.e. there are two motors drive two pressing roller separately, the turning speed synchronization of two rollers is rely on electrical control system.
The gearbox we used is of planetary kind, small volume, light in weight, load carrying capacity is high, the service life of gear and bearing is long. The machine adopt oil pool type lubrication method, equipped with lubrication oil cooling system. The system may adjust the cooling system as per varying of oil temperature, the machine will be shut off when the oil temperature reach settled value.
Output shaft of gearbox and input shaft of press roller is connected by expansion coupling, this ensured convenient disconnection, and make the two parts rigidly connected together, guaranteed reliable torque passing. The torque strength of expansion coupling must be strictly according to requirements. Before installation, the touching surface of output shaft and input shaft of press roller must be cleaned, all oil or grease must be removed.
Flexible coupling may ensure gearbox and pressuring moving in horizontal direction at the same time, good in adjustment.
Now, basically there are 3 kinds of motor for HPGR mill, i.e. squirrel-cage kind, YZR type and direct-current motor, the selection of motor should be according to the usage and requirement of HPGR mill.
Generally speaking, if the arrangement is goods, reach empty load startup condition, squirrel-cage motor is better, cheaper, simple structure and convenient in maintenance, direct current motor can be used only when the speed changing of roller is really required. For big size HPGR mill, due to big motor power, normally use YZR motor to decease the impact of power supply system during start-up.