Typical Flow Sheet of a Pelletizing Plant

Circular Pelletizing Technology
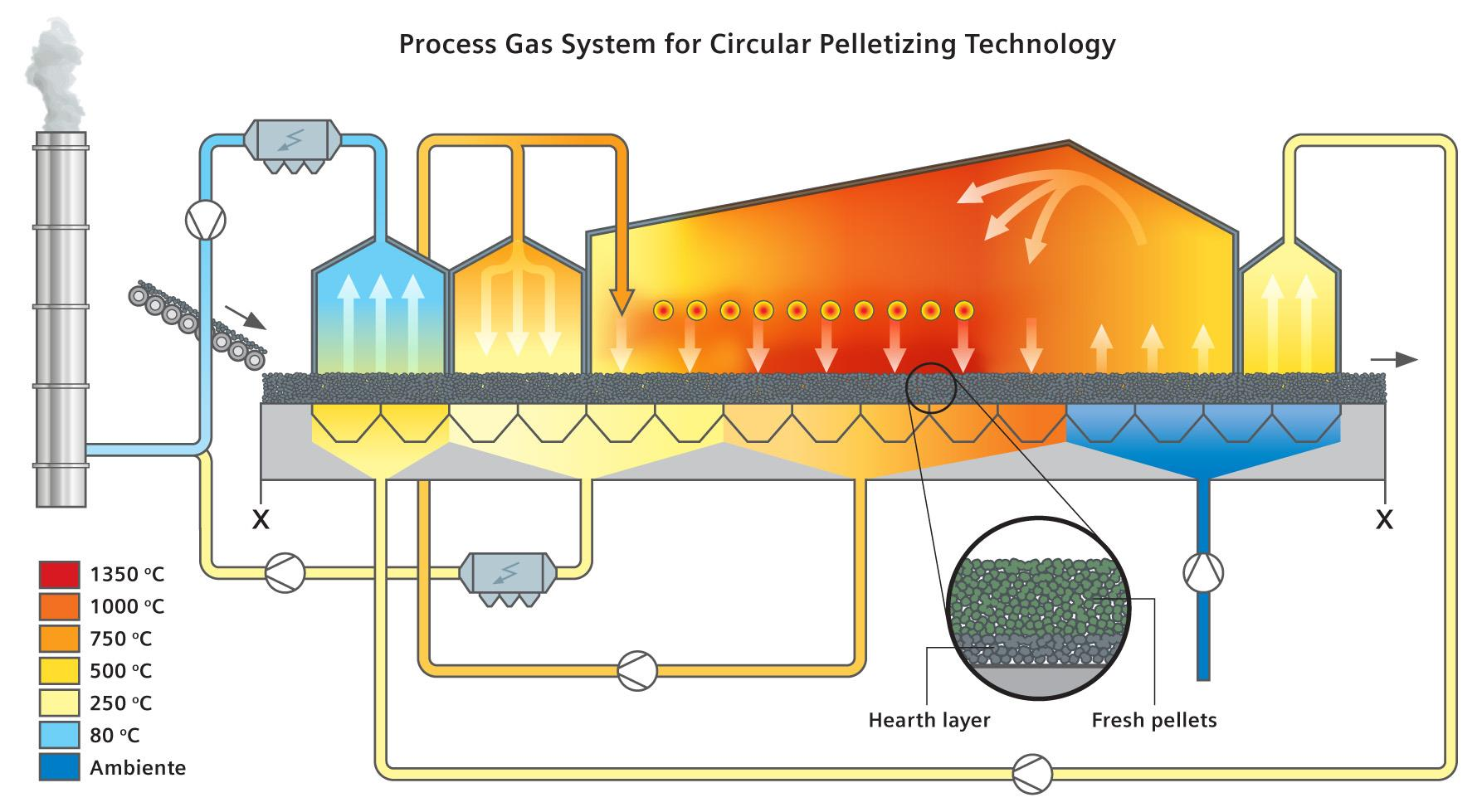
Comparison Of Different Pelletizing Plant
Type of Plant
Capacity Range
Technical Highlights
Straight grate pelletizing plants
1 – 6 Mt/year
pelletizing plants
- Low space requirement
- Low weight = low CAPEX
- Direct firing = low fuel consumption
- Simultaneous multi-fuel use
Circular grate pelletizing plants
0.5 – 2.5 Mt/year
pelletizing plants
- Compact plant design
- Proven and reliable equipment
- High compression strength
- Good reducibility of briquettes
Cold briquetting plants
0.05 – 1 Mt/y
- Advanced process simulation
- OPEX reduction
- Combination with eco solutions
- Utilization of steel works wastes
Advanced Pelletizing Technologies
Plant Design Optimization – Results, Findings
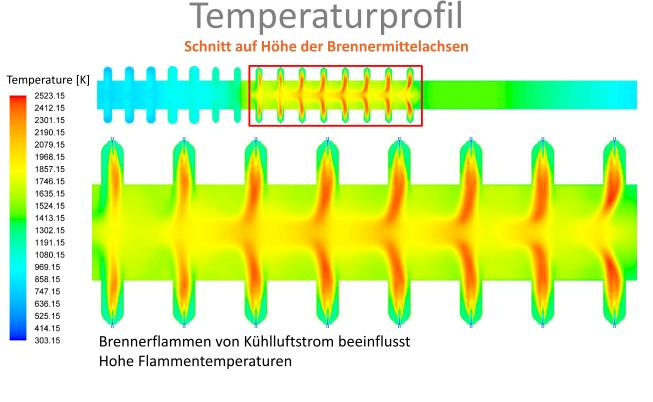
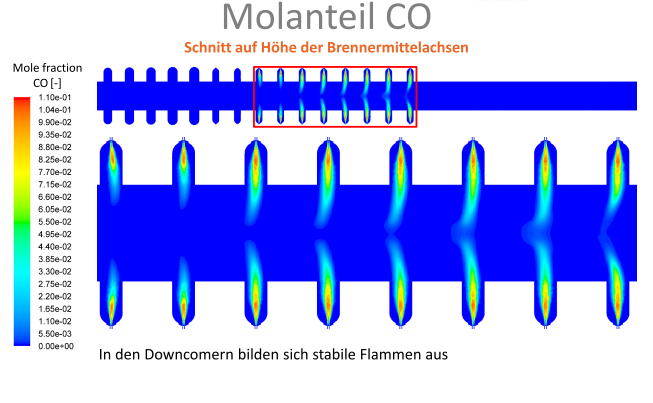
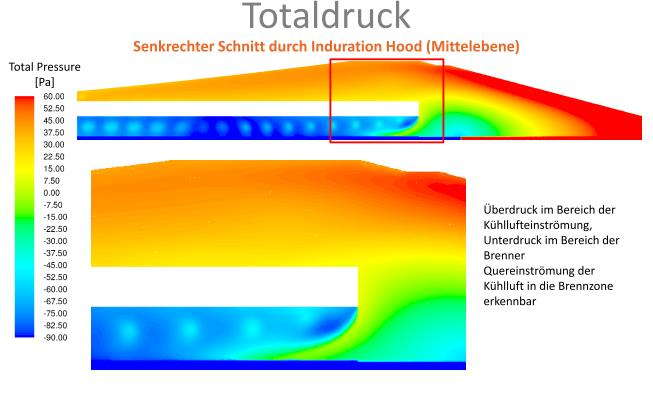
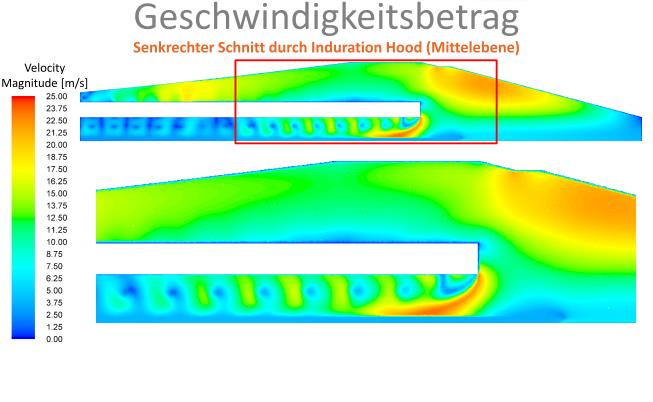
Technical Challenges During Engineering
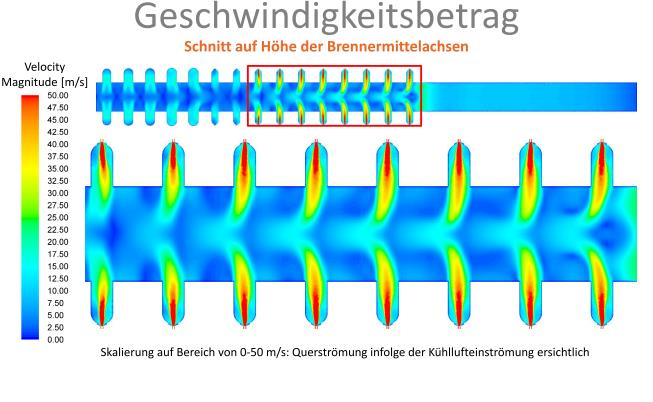
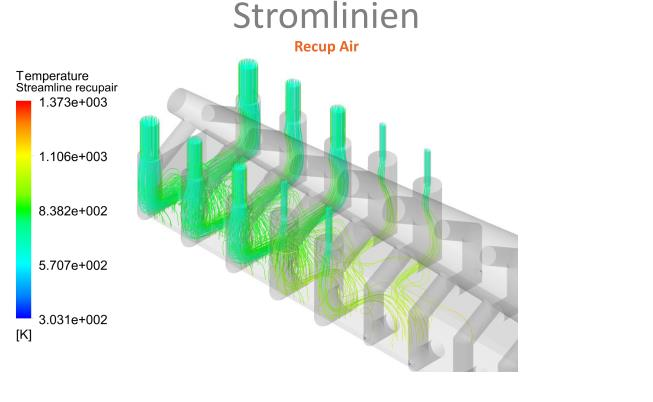
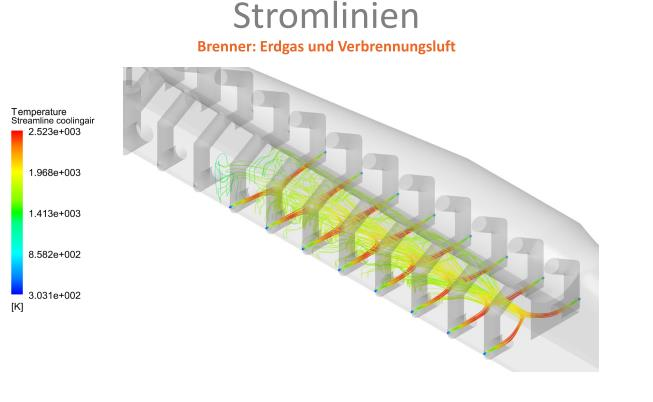
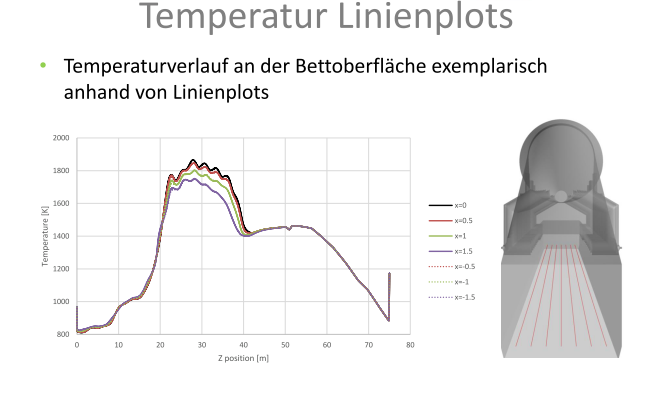
Development of Feeding Area
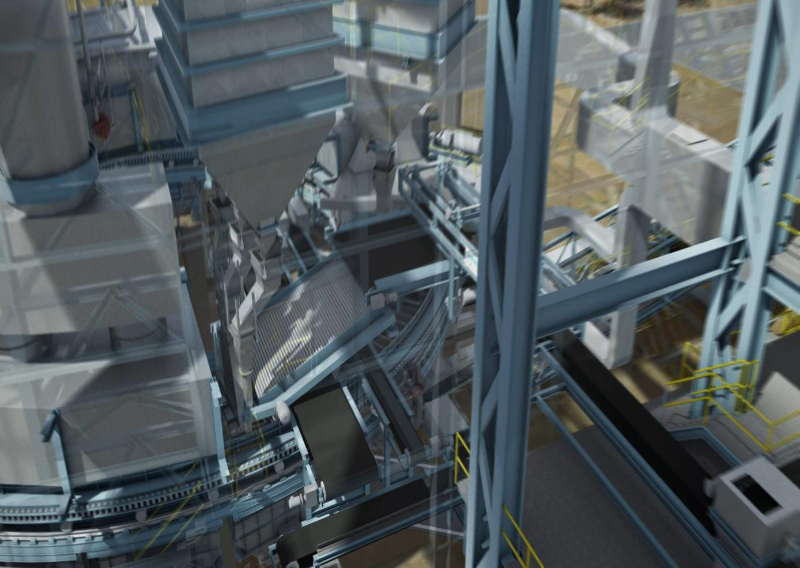
By speed variation of reciprocating conveyor more green pellets will be charged on outside than on inside in order to achieve level pellet surface.
Benefits of a CPT Plant
Compact plant layout, low building profile, short process air ducts, standardized equipment.
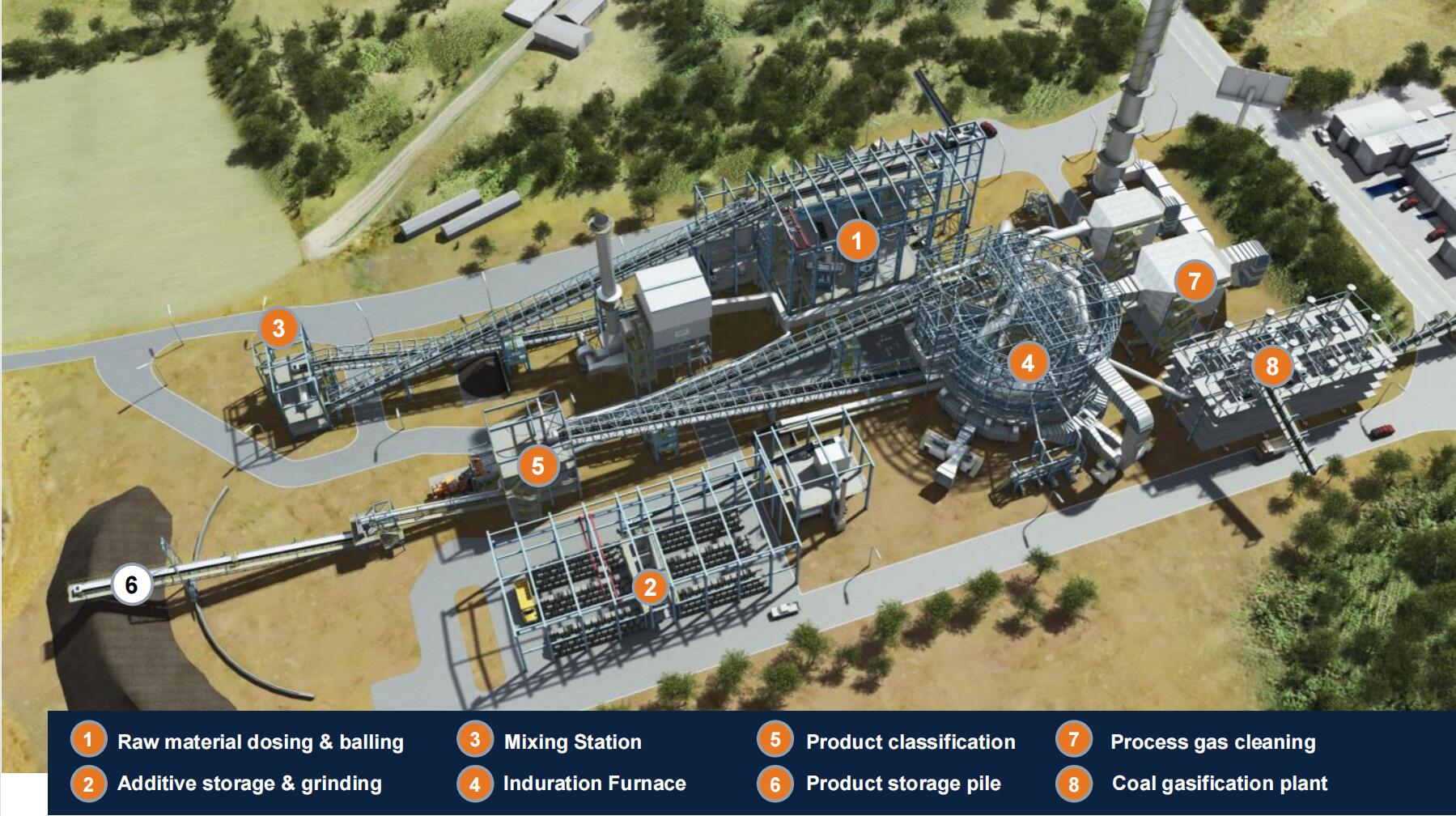
Low OPEX due to use of various energy sources: e.g. Coal Gas, PCI, COREX / FINEX Gas, Coke Oven Gas, etc.
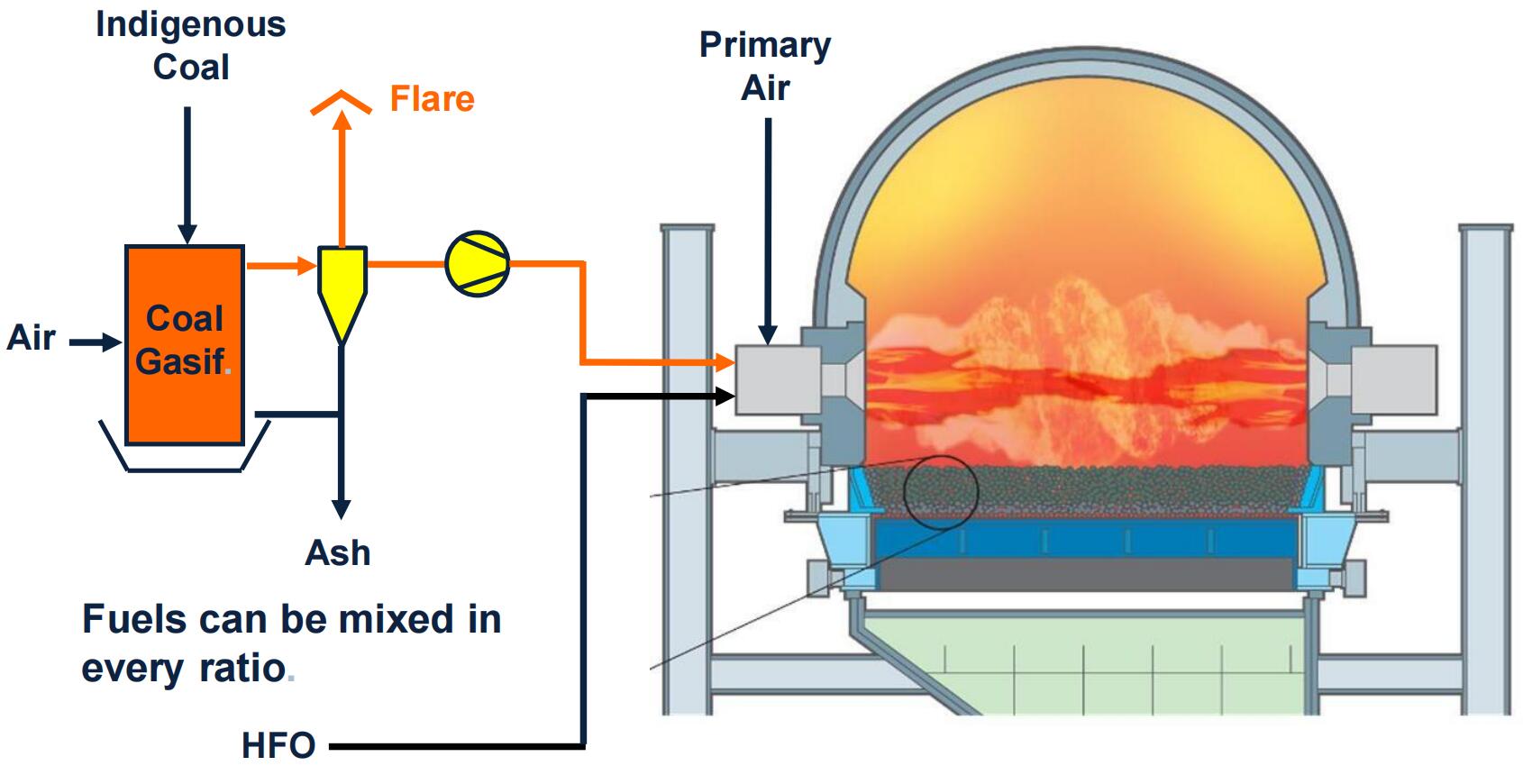
Environmental compatibility: 100% recycling of by-products, processing of in-plant waste materials
- Combination with MEROS Technology for Desulphurization of Waste Gas (Hydrated Lime or Bicarbonate based)
- Active Carbon Addition for Removal of Heavy Metals in Waste Gas
- Reduction of NOx by Ultra-Low-NOx Burner Technology or Selective Catalytic Removal
- Re-utilization of approx. 10 % of Steel Work Waste Materials in the Pelletizing Process
- Re-use of Pelletizing Plant Discharge Materials in the Pelletizing Process by Regrinding