The sinter machine is applicable to sintering operation of large-scale ferrous metallurgical sintering plants, and it is mainly applicable to the sintering treatment of iron ore powder in large and medium-sized sintering plants.
Main Data
- Effective sintering area: 75 square meters
- Effective sintering length: 30m
- Effective sintering width: 2.5m
- Center to center distance of head and tail sprocket: 42.745m
- Pitch circle diameter of head and tail star wheel: 2775.5mm
- Height of trolley breast board: 650mm
- Running speed of sintering trolley: 0.7 ~ 2.1m/min
Technical Description
Flexible Driver
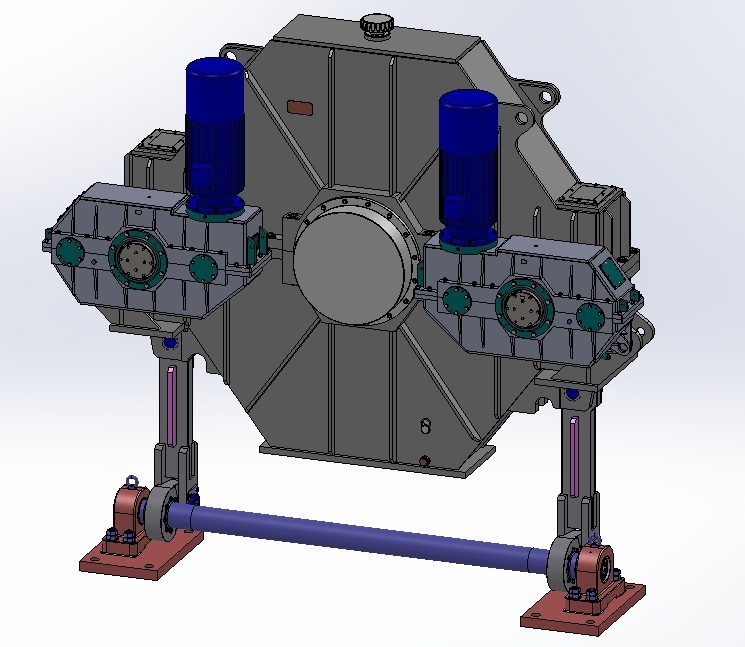
The driving device adopts multi-point meshing double drive full suspension flexible transmission.
The flexible transmission device adopts the expansion sleeve structure.
The height of the left and right bearings shall be adjusted for the assembly of the torsion bar, and the non coincidence of the centers of the left and right bearings shall be ≤ 1.0mm. The reducer adopts closed splash lubrication and high-precision hard tooth surface gears. All gears, gear shafts and ring plates are forgings.
Bottom Material Paving Device
The bottom material paving device is composed of feeding chute, middle chute, adjustment device of sector gate, swing funnel, vibration stop device, pressure sensor, etc.
The fan-shaped gate of the paving hopper is opened and closed by the on-site mechanism to control the feeding amount. The hopper is welded with angle steel to form the material lining, and the outlet of the fan-shaped gate is provided with wear-resistant lining plate.
The swinging funnel is of hanging type, and the funnel is of welded structure. The bucket is equipped with hanging manganese steel lining plate for easy replacement after wear. The thickness adjusting ram of the swinging funnel adopts the on-site adjusting structure, and the thickness of the paving material can be adjusted within the range of 20 ~ 100mm.
The funnel is supported at an eccentric position with its center of gravity. When the funnel swings forward occasionally, the funnel can automatically return to its original position due to the action of eccentricity.
In order to help the hopper reset, a counterweight is also set. If there is foreign matter on the trolley (sinter or broken grate), the swinging bucket will swing towards the forward direction of the trolley with the support shaft as the center. After the foreign matter passes through, the counterweight can reset the hopper.
Mixture Feeding Device
The feeding device is composed of material trough, round roller feeder, nine roller distributor, breathable rod device, leveling device and grate roller pressing device. The center of the funnel and the center line of the round roll are staggered by 100mm to prevent natural blanking between the funnel outlet and the round roll.
The material trough lining plate laid in the large material bin adopts anti sticking material lining plate with a thickness of 20mm. The auxiliary gate of the feeding gate is controlled by electro-hydraulic push rod, and each auxiliary valve can adjust the stroke separately to realize the function of adjusting the thickness of the material layer.
In order to greatly reduce the problem of mixture sticking in the silo, the four corners of the silo adopt circular arc elliptical structure.
The round roller is of welded structure and trunnion flange type. The surface of the round roller is lined with 16mm stainless steel lining plate, and a cleaner is installed on the other side of the feeding direction of the round roller to scrape off the mixture adhered to its surface at any time.
The sweeper (divided into 4 sections along the length) realizes scraping by pressing the wear-resistant rubber scraper with spring. The round roller device adopts variable frequency speed regulating motor (with speed measuring encoder), so that the round roller speed can be adjusted steplessly within a certain range.
In order to prevent the mixture from being compacted tightly when it falls, a two-layer structure vent rod device is set, which is made of stainless steel. The vent rod is installed in the lower middle of the loading layer of the trolley and fixed on the framework of the sintering machine.
The mixing silo is equipped with a mixture steam preheating device to improve the temperature of the mixture.
Nine Roller Distributor
The roller distributor is set, which adopts the single roll single action transmission mode, the number of motors is 9, and the roller body is made of stainless steel.
Retaining plates are set on both sides of the roller, and the parts or components used have good interchangeability to realize segregation distribution. The roller distributor is composed of a plurality of stainless steel round rollers with anti sticking materials, a baffle plate, a base, a motor reducer, etc.
The single roll single drive type has simple structure and is convenient for maintenance. Motor power 9×2 2Kw。 The distributor is required to be able to adjust the angle at any time.
Head Star Wheel
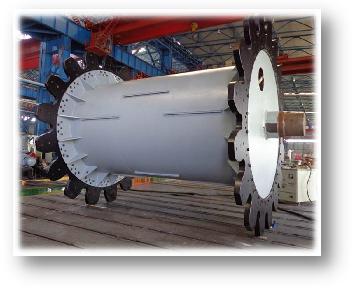
The head star wheel is trunnion type, the middle part is star wheel drum and toothed plate, and the two ends are trunnions. The shaft is welded with the star wheel drum, and the trunnion is made of 35 forged steel.
The tooth plate is made of 50Mn (surface quenching hrc50-58, depth 3-5mm) or nm400. The toothed plate is double toothed plate and triple toothed plate. The tooth profile of the toothed plate shall be machined by NC machine tool to ensure interchangeability. The toothed plate is connected to the web plate of the cylinder block by block through reamed bolts and high-strength bolts. The normal service life of the toothed plate shall not be less than 5 years.
After the head star wheel is manufactured, it shall be pre installed in the manufacturer.
A bulk material collecting cylinder is arranged on the outer circumference of the star wheel cylinder to recover the bulk material dropped by the trolley in the overturning process. The dust collected by the belt conveyor and discharged into the dust hopper can be avoided.
Self aligning spherical roller bearings with retracting sleeve structure are installed in the bearing seats on both sides of the star wheel. The bearing pedestal on the drive side is the fixed end and the bearing pedestal on the other side is the free end.
The bearing seat at the free end can be moved longitudinally along the sintering machine through the hydraulic jack, so as to realize the deviation adjustment of the trolley.
The two pole protection device of limit displacement travel switch of flexible transmission device can effectively prevent equipment accidents.
Tail Moving Frame
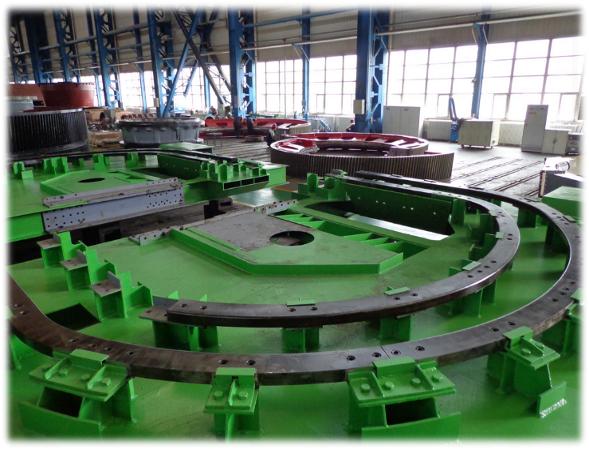
The tail device includes tail star wheel, moving frame, supporting wheel group, ash discharge device, tail bend, balance device, hydraulic adjustment device, etc. the whole device is suspended on the tail frame through the support of supporting wheel group on the tail frame, and can move back and forth along the horizontal direction to absorb the elongation of trolley due to heating and other factors.
The tail star wheel is of through shaft type, the main shaft is made of 45 forged steel, and the quenching and tempering treatment is 207hbw-241hbw. Ultrasonic and penetrant flaw detection must be carried out before and after finishing, and no defects affecting the strength are allowed.
After the star wheel is welded, it shall be annealed to eliminate the stress, and then it can be machined.
The normal service life of the toothed plate shall not be less than 5 years
After the toothed plate is assembled with the star wheel cylinder, the toothed plates on both sides shall be synchronized, and the misalignment error of tooth profile on both sides shall meet the design requirements.
When assembling and welding the side plate of the tail mobile frame, the welding deformation of the side plate shall be controlled, and the overall stress relief treatment shall be carried out after welding. The size and bending deformation of each part of the side plate shall meet the design requirements.
The upper frame of the moving frame at the tail of the sintering machine will be made into assembly parts, which will be transported to the site for installation after assembly and alignment in the factory. This can ensure the accurate relative position between the upper frame and the side plate and facilitate installation.
The tail star wheel is supported on the moving frame through the bearing seat of the spherical roller bearing with the return sleeve structure. The star wheel web plate is a welded assembly, which is assembled on the through shaft through the hook wedge key. The tooth plate adopts the star gear plate at the tail of sintering machine with modified tooth arc curve to reduce trolley arching. The tooth plate is connected to the star wheel web plate one by one with hinged bolts.
The mobile frame is composed of upper and lower frames, side plates and bends. It is suspended on the frame at the tail through the support of the left and right idler rollers. The upper and lower four guide wheels make the mobile frame move only horizontally in the longitudinal direction to absorb the thermal elongation of the trolley. The normal service life of the bend shall not be less than 3 years, and the upper and lower frames and side plates are ordinary carbon steel weldments.
In order to collect the bulk materials during the unloading of the trolley, an ash discharge device composed of a receiving hopper, a rotating bucket and a fixed bucket moving horizontally with the moving frame is set, so that the bulk materials can be smoothly discharged into the unloading bucket under the machine. Each ash hopper is of welded structure, and the interior of the fixed hopper is provided with wear-resistant lining plate and material lining.
The counterweight is composed of pulley, chain, counterweight, counterweight dust shield, etc. the moving frame is tightened towards the machine head through its counterweight, so that each single trolley forms a continuous conveyor belt, which plays the role of squeezing the trolley, so as to reduce the air leakage and material leakage in the workshop, and eliminate the grinding and impact of the trolley during operation.
The use of appropriate counterweight can make the mobile frame automatically adjust with the change of temperature during the operation of sintering machine, and avoid the accidents such as trolley rail clamping and deviation. The upper part of the counterweight chain is provided with an anti ash cover to prevent the surface area of the sprocket and chain from being dusty.
In order to meet the needs of installing the trolley and taking out the trolley during maintenance, a hydraulic adjustment device and a safety travel switch are set on the tail frame.
The material of the tail bend is 50Mn (overall quenching and tempering 230 HBW – 270 HBW, working face quenching) or nm400.
The toothed plate is made of 50Mn (surface quenched hrc50-58, depth 3-5mm) or nm400, and the toothed plate is double toothed plate and triple toothed plate.
Pallet Car
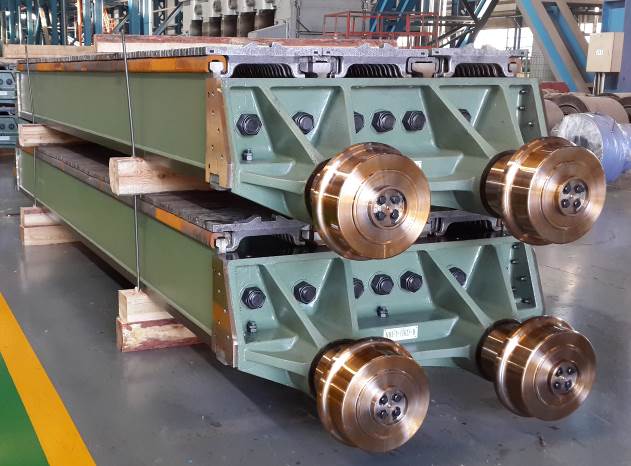
1) Pallet Car
The pallet car is mainly composed of body, breast board, elastic sealing traveling plate, thermal insulation parts, traveling device, etc. The body adopts an integral structure. The body is made of special nodular cast iron.
The breast board is composed of upper breast board and lower breast board. The sealing device of pallet car is assembled at the lower part of both sides of body with bolts. The table body, breast board and heat insulation board are made of special nodular cast iron.
The mechanical properties, chemical composition, spheroidization rate and heat treatment flaw detection must meet the design requirements. The spheroidization rate of platform body and breast board shall be ≥ 85%, and the spheroidization rate of thermal insulation parts shall be ≥ 80%. The wheel tread must be medium frequency quenched. There should be a report of physical and chemical inspection.
The body is an integral structure. The axis lines of the four axle holes shall be in the same plane, and the different flatness error shall not be greater than 0.12mm. The coaxiality tolerance of the axis lines of the two concentric axle holes shall not be greater than 0.05mm, and the parallelism tolerance of the axis lines of the two pairs of coaxial holes shall not be greater than 0.1mm. The axis lines of the axle holes shall be called on the central plane of pallet car body, and the symmetry tolerance shall be 0.05mm. Cracks, porosity and other defects on the surface of the casting pallet car that affect the strength of the casting shall not be eliminated.
The bolt holes on the car body and breast board are processed by die drilling.
After the pallet car is assembled, the wheels shall rotate flexibly without jamming and shaking. The four wheel axles and the vehicle body shall adopt interference fit to ensure their interference and prevent the axle from loosening.
First, trial produce 1 ~ 2 pallet cars, and batch production can be carried out only after passing the inspection.
The pallet car roller adopts solid self-lubricating sliding bearing.
The end of the pallet car body is embedded with a replaceable wear plate.
Normal service life of pallet car body: more than 5 years, and there shall be no waist collapse, girder crack and other problems within 5 years.
2) Pallet car body:
The pallet car body adopts special nodular cast iron. 1-2 trolleys shall be produced according to the drawing, and can be put into mass production only after passing the inspection. Wear plates are installed at both ends of pallet car.
3) Breast board:
The breast board adopts special nodular cast iron and must be annealed at high temperature.
4) Grate bar:
The grate bar is made of rtcr28ni, and its service life is 8 months after normal production.
5) Pallet car assembly:
The contact between the bearing sleeve and the inner hole of the wheel shall be uniform, and the assembly of the wheel and rolling sleeve shall be flexible. Before leaving the factory, the wheel shall be filled with 2 / 3 lubricating grease and can rotate by hand.
After pallet car is installed, the test inspection shall be carried out (trial assembly shall be carried out after the prototype is processed and manufactured, and mass production can be carried out only after it is qualified). The pallet car shall ensure that the four wheels of the trolley are in uniform contact with the steel rail and meet the relevant design regulations.
Place the four wheels of pallet car upward, and check the working surface between the wheels. It is required to be in the same plane, and the allowable error is 0.25mm.